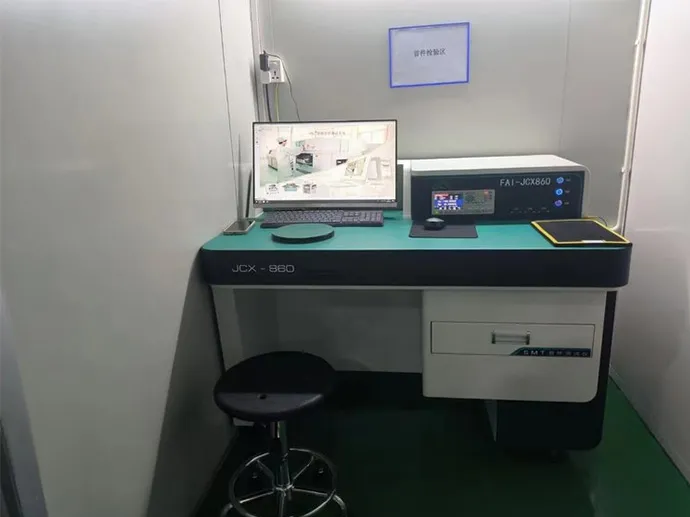
Supplier Management
The company has set up a Supply Chain Audit Department to conduct a comprehensive assessment of suppliers' qualifications, product quality, production environment, etc., to screen out qualified suppliers with reliable quality and ensure their ability to provide products and services that meet the quality requirements.
Regularly evaluate and audit the suppliers to ensure that they continuously meet the quality requirements.
Establish mutually beneficial relationships with suppliers to jointly identify and respond to risks in the supply chain.
Purchasing Control
Formulate procurement control procedures to clarify the quality requirements of purchased materials, supplier evaluation, and auditing standards.
According to the relevant national standards and technical specifications, carry out strict incoming inspection of purchased raw materials and components to ensure that the quality of goods meets the standard requirements, the specific inspection standards include but not limited to the following aspects:
Appearance quality
Observe the product appearance, material and assembly quality with naked eyes. Check whether the appearance of the product is complete, without obvious defects, damage stains, etc..
Size and weight
Use measuring tools to measure parameters such as size and weight. Measure and check whether the size and weight of the product meet the design requirements and specifications.
Functional performance
Functional performance tests are conducted on the products to evaluate the performance of the products in different usage scenarios to ensure that the products can work properly and meet the expected usage requirements.
Material and assembly quality
Check whether the material and assembly quality used in the product meet the requirements, and whether there are problems such as looseness, missing parts, and poor quality.
Safety performance
Combined with relevant safety standards, adopt safety performance testing equipment and methods to test the safety performance of the product (battery), including electrical safety, mechanical safety, chemical safety, and other aspects.
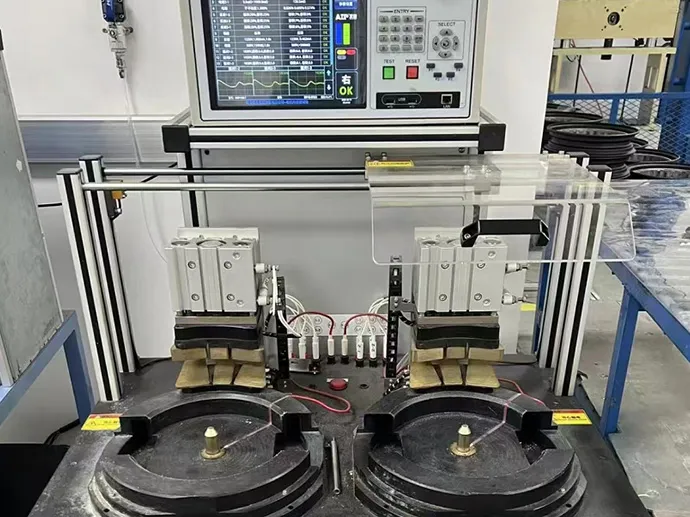
Production quality standards
Our company has formulated a perfect quality management process, which is refined to each production link and interlocked to ensure that each link has clear quality requirements and inspection standards. Including but not limited to product qualification rate, customer satisfaction and other quality objectives, as well as the corresponding quality standards, such as product performance indicators, appearance requirements.
Equipment maintenance and calibration
1. Regular maintenance: regular maintenance and maintenance of production equipment, including equipment cleaning, lubrication, debugging and other daily work, to ensure that the equipment has been in the best operating condition.
2. Equipment calibration: Regular calibration of production equipment to ensure its normal operation and reduce product quality problems caused by equipment failure.
Real-time monitoring
Utilizing sensors, monitoring systems, and other modern technical means of regular or irregular quality testing, real-time monitoring of key parameters in the production process, and once abnormalities are found, take immediate measures to adjust.
Data analysis
Collecting and analyzing quality data, constantly looking for opportunities to improve the production process, to improve product quality and production efficiency.
Non-conforming goods control
Formulate the process of handling nonconforming products, including isolation, labeling, recording, and rectification of nonconforming products. Analyze the nonconforming products, find out the reasons, and take measures for correction and prevention.
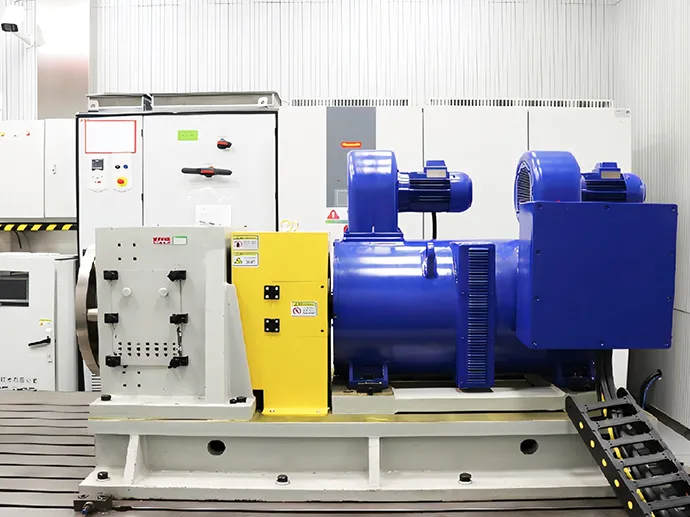
Submit application
The production department applies for inspection to our internal quality inspection department, fills in the inspection application form, and attaches the relevant information and parameters of the product, so that the inspection department can verify one by one.
Product Inspection
Each product will be inspected in detail, including but not limited to product quality, specifications, packaging, and so on. The inspection process will scrutinize the customer's requirements for the product and packaging, and will be based on relevant standards and inspection methods.
Quality and safety inspection
Appearance Inspection: Check whether the appearance of the product is intact, such as color, size, welding, etc. whether it meets the customer's requirements.
Performance test: According to the characteristics of the products, carry out the necessary performance tests, such as function test, torque test, dynamic balance test, etc.. The testing methods will be different for different products, for example, the electric transaxle products, the commonly used testing methods are: spectral analysis, ultrasonic testing, three-coordinate measurement, torque testing machine, dynamic balancing machine test and so on.
Safety testing: to ensure that the product meets the safety standards, such as electrical safety, chemical safety, biological safety and so on.
Packaging Inspection
Check whether the product packaging is intact, moisture-proof, damage-proof, etc. Confirm whether the packaging meets the standards of the exporting countries and the needs of customers.
Confirm whether the markings on the products or packages are clear and accurate, including product name, specifications, production date, shelf life, manufacturer, and other information.
Record
Record all inspection data and results, form a complete product inspection report, and send it to the customer together with the product.
Continuous improvement
Establish a continuous improvement mechanism to identify improvement opportunities and implement improvement measures through data analysis, internal audits, and management reviews.
Regularly evaluate and review the effectiveness of the quality management system to ensure that it continues to meet the standard requirements.